Finite element damage prediction of composite structures
Texte intégral
Figure



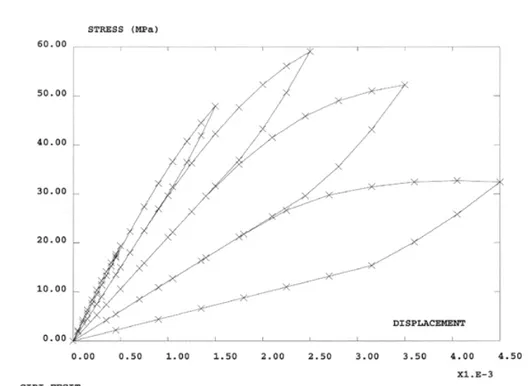
Documents relatifs
The effective elastic moduli of three-phase composites, composed of a ductile matrix, randomly located yet unidirectionally aligned circular fibers, and voids, are derived by using
Probabilistic analysis is performed using Monte Carlo Simulation (MCS) on a refined composite plate finite element model to calculate statistical properties of the
In the current study, a micromechanical model based on transformation field analysis been used to quantify the overall material properties of electrically active
This review will emphasize the roles that AE can play as a tool for the composite materials, damage mechanisms, and characterization of damage evolution with increasing time or
6th International Conference on Green Energy and Environmental Engineering GEEE-2019 As mentioned previously the amount of AE energy recorded during the failure is expected to
Abstract : The aim of this work is to introduce a new approach for clustering acoustic emission data occurring during the fracture process of glass fibre reinforced polymer
The tufted plates subjected to short-beam shear tests aided especially in the behavior analysis of tufting density and angle in mode II loading condition, while
LMS Samtech Samcef efficiently answers these industrial concerns with features such as easy definition of cracks and delamination zones; estimation of the propagation load via